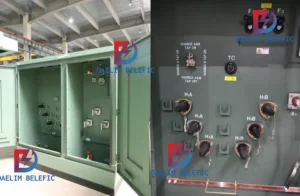
How to Choose Pad Mounted Transformer?
Table of Contents Selecting the right pad-mounted transformer requires careful consideration of several critical
ELECTRIC, WITH AN EDGE
There is a growing focus amongst professionals on the correct disposal of electrochemical power storage power plants, the full lifecycle prices included, and security problems. This marks a shift away from the gradual adoption of lifecycle theory in noncombatant sectors, with a preliminary emphasis on its use in tasks to assess construction costs.
Nuclear power plant for storing energy are developed to hold extra power generated when demand is low and to launch it when need is high. These plants are vital for preserving grid stability and taking full advantage of the application of renewable resource sources. Let’s explore this concept additionally.
Pumped Hydroelectric Storage (PHS): This is the most common type of grid power storage. It involves two water reservoirs positioned at various elevations. Throughout periods of reduced power demand, excess electrical energy is made use of to pump water from the reduced to the top tank. When there’s a higher need for electrical power, water is launched from the upper tank to the lower one, travelling through generators, generating electrical power while doing so.
Battery Energy Storage Systems (BESS): BESS utilizes chemical batteries, such as lithium-ion, to keep and launch electricity. They provide fast action times and are ending up being increasingly prominent because of the lowering price of batteries and their capability to be situated more detailed to require centers.
In Compressed Air Energy Storage (CAES systems), excess electrical power is made use of to pressurize air, which is ultimately kept in below ground dental caries. When there is high demand for electrical energy, the pressurized air is launched, heated, and increased in a generator to produce power.
Power can be saved through thermal ways, which includes keeping it in the form of heat or cold. A prime example of this approach is using liquified salt, which can be warmed and stored in shielded tanks before being utilized to produce vapor that drives generators and produces electrical energy when needed.
Flywheel power storage space involves saving energy as rotational power in a spinning flywheel. When there is excess electrical energy, it is made use of to speed up the flywheel. Later on, when electrical energy is needed, the kinetic energy stored in the spinning flywheel is transformed back into electrical power.
Grid Stability: They assist support the grid by stabilizing supply and demand, decreasing the possibilities of blackouts or brownouts.
Combination of Renewable Energy: Renewable resources like solar and wind are recurring. Storage space systems make certain that energy is available also when the sun isn’t shining or the wind isn’t blowing.
Height Shaving: By launching stored power throughout peak need times, these plants reduce the requirement for expensive peak power plants.
Support for Distributed Energy Systems: They can be coupled with regional renewable energy resources in microgrids to provide power to remote locations.
Expense Savings Through Smart Energy Management: These facilities can help maintain energy prices and supply power at a lower price by keeping energy throughout durations of low need and releasing it throughout durations of high demand, therefore lowering the general energy expenses.
The globe’s energy scene is changing drastically. With the rise of renewable energy resources, the value of energy storage centers in keeping a trustworthy power grid is essential. This item supplies a detailed evaluation of the prices associated with operating these plants over their lifetimes, providing important details for those associated with this elaborate field.
Nuclear power plant that keep power, especially those utilizing electrochemical methods, are ending up being a viable solution for taking care of the uncertain accessibility of renewable resource resources. These plants save extra energy when manufacturing is high and release it when there is a scarcity, leading to a reputable electrical power supply.
A certain scenario to think about is the change towards renewable resource. Image a city that depends greatly on solar energy. When the sun is shining, the photovoltaic panels produce surplus power contrasted to the city’s usage. Nonetheless, on cloudy days or during the night, there is a deficiency. In such cases, power plants developed for power storage play an important duty by saving added power and providing it when the solar panels are not generating sufficient.
A recent research showed that cities transitioning to renewable energy resources without appropriate power storage space dealt with 30% higher energy expenses due to the demand to get power during shortages. Nonetheless, cities with efficient power storage nuclear power plant managed to minimize this added cost by approximately 70%.
The combination of energy storage facilities can considerably decrease the expenses incurred throughout the shift in the direction of renewable energy resources by giving a trusted power supply, irrespective of the production capability of sustainable resources.
Core Concept: Emphasizing Life Cycle Expenses power storage space power plants to is necessary to take into account the complete life cycle costs, beyond simply the preliminary capital outlay. This includes costs related to design, maintenance, and decommissioning.
In a particular situation where a coastal city is preparing to facility, the preparation phase harsh impacts of deep sea. It is essential to select materials that can hold up against rust, even if they are pricey at first, as they can eventually cause savings on upkeep costs over time.
Checking out similar coastal centers’ data, we found that choosing corrosion-resistant products results in a 15% hike in initial expenditures. Nevertheless, this financial investment enjoys long-term benefits, as upkeep expenses over 20 years stop by 40%, inevitably producing significant monetary gains.
Integrating forward-thinking designs, particularly in difficult environments, can lead to higher preliminary costs but results in considerable savings over the life cycle of the energy storage nuclear power plant.
The short article will certainly be continued in the following couple of dialog boxes as a result of its length. Please proceed to the next box to read the remainder of the material.
The building and procedure phases form the core of the life cycle of power storage power plants. Costs incurred during these phases usually represent the mass of the entire life process expenditure.
Think about an energy storage nuclear power plant being constructed in a densely inhabited urban area. Building and construction obstacles such as limited space, sound limitations, and transport of heavy materials in busy streets can blow up expenses. In addition, throughout its operation, the plant needs to meet stricter emission and safety criteria as a result of its area.
Information from recent jobs indicate that creating power storage power plants in urban locations can be 25% extra costly than in country settings. Furthermore, functional expenses in cities, considering more stringent guidelines and even more regular examinations, can be 15% greater on an annual basis.
While metropolitan setups use closeness to major power consumption centers, they include their very own collection of difficulties and costs. It’s crucial to factor in these additional costs when planning for power storage space nuclear power plant in such atmospheres.
Taking care of the end-of-life expenses for power storage centers is an important aspect that should not be disregarded. This phase includes the costs connected with dismantling, recycling, or removing parts, and it plays an essential duty in maintaining ecological sustainability.
A city plans to deactivate a 30-year-old energy storage power plant. This entails safely taking apart facilities, reusing recyclable products, and securely disposing of contaminated materials, like battery acids. The proximity to residential areas likewise means the disposal process have to be non-disruptive.
Based on a recent study of similar deactivating undertakings, it was located that the disposal phase might constitute around 10% of the overall expenditures incurred throughout the plant’s life process. Additionally, not abiding by environmental regulations throughout this stage can cause fines that include in the costs.
While much focus is provided to the layout, building, and procedure phases, it’s equally essential to prepare for the end-of-life phase of energy storage nuclear power plant. By doing so, cities and companies can prevent unanticipated prices and guarantee they comply with ecological standards.
Simultaneously, the full lifecycle cost concept started to be used in the power industry. Some experts started checking out the power systems of cities or metropolitan areas and ultimately performed a complete lifecycle price study of crucial equipment or systems. Currently, the complete lifecycle price theory has formed a relatively mature theoretical system and has actually been widely used in fields such as air travel, telecommunications, healthcare, production, and construction. In addition, domestic experts have basically reached an agreement that applying the full lifecycle expense concept in the power market can properly make sure economic feasibility while making certain safety.
The complete lifecycle phases of an electrochemical energy storage power plant can be divided right into design, construction, procedure & upkeep, and disposal stages. As a result of characteristics such as the gradual capability decrease during the power plant’s lifecycle, capability deterioration impacting power storage space performance, and energy losses throughout the conversion process, the operation and upkeep stage’s prices consist of not just upkeep but additionally substitute and power loss costs. Because the energy storage nuclear power plant might trigger environmental pollution at the end of its life and call for taking down, the opportunity of reusing rare-earth element resources for reuse makes the disposal phase and its linked costs a substantial part of its lifecycle.
The very first phase in the full lifecycle of an electrochemical energy storage nuclear power plant is the design stage. It usually comes after site option research study and includes usefulness researches and comprehensive design jobs. Thus, style costs can be divided into expediency research study costs and certain style costs.
“Unlocking the Secrets of Memory: A Breakthrough in Neuroscience”
Where:
C = Total design expenses
C = Feasibility research study expenses
G jsD = Specific style prices
During the building and construction stage, firms consider first investment prices that encompass design and construction expenses. This phase largely entails getting or renting land, creating various frameworks like buildings and installments, acquiring hardware devices and software program, establishing systems, hiring supervision and bookkeeping firms, and taking care of tax. Organization models differ, however expenses are generally categorized into infrastructure and IT equipment & software application. Energy storage power plants have a 25-year functional duration and need fairly small acreage, resulting in land leasing based upon building and construction and operational durations. Working with supervision and auditing firms incur fairly inexpensive, which can be organized with other organization tasks. Thus, these prices can be merged right into groups such as land leasing, infrastructure building, equipment & software application purchase, installation, tax, and others.
[Cz = C + Cic ss + C + C az +T js + C ]
The formula includes a number of variables, including Cz, which represents the total building and construction costs.
To be particular, renting land is foundational for constructing energy storage space nuclear power plant, and land costs often rise and fall with market problems. With increasing future land need and diminishing available areas, land expenses might potentially increase. The leasing cost for land can differ dramatically depending on the place of the energy storage power plant. Costs for land are established by the rented location and device leasing price.
“Critical Thinking Skills Boosted by Spatial Reasoning and Problem-Solving Abilities”
Leased location is stood for as S td, while the unit renting price
In the context of power storage power plants, efficient price monitoring hinges on the reliable building and construction of framework, procurement, and setup of hardware and software. These components commonly account for a significant section of the general construction prices and are typically calculated based on quantity and acquisition rate.
During the 3rd phase of the electrochemical energy storage space plant’s life process, it gets in the procedure and upkeep stage, which lasts the lengthiest and is commonly referred to as the operational duration. This phase generally spans 25 years.
During the operation and maintenance stage of various tasks, the emphasis gets on taking care of intricate tasks connected to framework, equipment, personnel, and power grids. This phase entails fixing and keeping facilities, tools, and batteries, as well as hiring and taking care of personnel for everyday operations. In addition, activities consist of managing electricity usage, following sending off agency directions, and taking care of economic responsibilities such as tax obligations and car loan repayments.
The malfunction of the price of operating and keeping an organization, based on an extensive evaluation of its numerous activities, includes replacement expenses, energy loss expenses, and expenses associated with operation and maintenance (O&M) The O&M prices, subsequently, are composed of repair service expenditures, labor expenses, economic costs, tax obligations, administration costs, and various other miscellaneous O&M expenses. It’s essential to note that the devaluation expense, which is reflected in the purchase and installment cost of set assets throughout the building stage, will not be included in the procedure and upkeep phase.
G;= Gth + (sh + Cu + Crg + Cau +Tyu + Cg. + Cgtyw) x Nyy
The electrochemical power storage plant’s operating and upkeep prices (C) are made up of numerous parts. These include the expense of power loss each year (C1), the expense of repairs per year (C2), the substitute price (C3), and the price of labor annually (C4). Furthermore, there are annual finance prices (C5), taxes (T), administration costs (C6), and other various overhead (Cn) annually. The total cost of ownership is calculated over the plant’s functional cycle (N).
1. Replacement cost. Substitute cost describes the core part of electrochemical energy storage power plant battery, as a result of life reasons, the requirement to set up a defined interval or defined number of cycles to be replaced when reached, and its substitute of the battery generated by the purchase of batteries, removal of batteries, setup of batteries, and various other all prices. In electrochemical energy storage, as a result of the efficiency characteristics of the battery brought on by the use of the procedure will progressively decline, when the decline to a certain extent demand to be replaced. The life of a battery is normally determined by two indicators, namely, age and variety of cycles. Reaching a specific age or capability degeneration to a certain percentage of the power offered by the battery and the conversion efficiency will certainly be reduced or can not be used, in order to safeguard the electrochemical energy storage power plant secure, secure and reliable operation, usually need to be replaced. The number of cycles is a special technical indicator for electrochemical energy storage, i.e., a complete charge and a discharge are considered as one cycle. Although electrochemical energy storage space does not run at complete cost and discharge each time, it can be likewise transformed according to the degree of procedure. When the number of cycles gets to the life limitation, the positive and adverse electrode products are used up and can no more be used. The number of cycles when the ability decreases to a specific percentage is the total number of cycles of the battery in an electrochemical power storage plant, and this percent varies among different modern technology courses. The variety of years and the variety of cycles together identify the particular time of cell substitute in an electrochemical power storage space plant, but the number of years is typically a lot longer than the variety of years calculated by the variety of cycles, so the variety of cycles is picked to stand for the index. Battery replacement is when all the batteries are repurchased for installment.
Ntn = Nyy/Nsy (8 ).
Ninth Grader Solves Math Problem in 365
Cth = National Pattern Q (10)
Where, N. represents the number of substitutes; N represents the operation cycle of the electrochemical energy storage power plant; N represents the battery use cycle; N. signifies the complete number of cycles; Nm represents the variety of cycles per day; P signifies the purchase cost of the unit ability of the battery cell (consisting of the purchase, setup, taking down, etc); and 0 denotes the mounted capability.
The expense pertaining to power loss in electrochemical energy storage systems involves charging and discharging processes to save energy. Charging includes buying power from the grid, while discharging involves offering power back to the grid. Charges are incurred for charging from the grid and gaining feed-in tariffs for discharging. Settlement in between the nuclear power plant and the grid typically concentrates on price differences, identifying the earnings for the power plant. In calculating the life cycle cost, it is important to think about power loss costs incurred throughout the charging and discharging procedure as a result of variables like core exothermic line losses. These costs are affected by billing power, charging tolls, and the power conversion performance of the storage plant.
Csh = Qcd Ped-( 1- Ry) (11)
D where 0. denotes the billing power; P signifies the charging tariff; and R. denotes the power conversion performance of the electrochemical energy storage plant.
The total expense required to bring back the electrochemical energy storage plant to its typical operating condition, consisting of maintenance, material, and insurance coverage prices, is described as the repair work price. Throughout the pre-construction decision-making procedure, these prices are commonly determined independently. The maintenance price is established by the initial value of set properties and the upkeep price, while the product expense is determined based on the set up capacity and product cost allocations. Insurance coverage costs are identified by the initial value of fixed possessions and insurance policy prices. Prior to building, the upkeep rate and product price flat rate are utilized to approximate the prices. The equation for computing the repair service price is Cxi = Cwx + Ca + Cox (12 ).
Equation relating Cwx and FA-Rwx.
Ca =. Va (14 ).
Cbx = FA- Rbx (15)
where C represents upkeep expense; C, signifies product cost; C represents insurance coverage price; FA represents original value of fixed assets; R. represents upkeep rate; 0 denotes installed capacity; U, denotes product price level price; and R represents insurance coverage price.
Labor expense. Labor price describes the repayment to the electrochemical energy storage nuclear power plant worker salaries and benefits, including all technical, managerial and other electrochemical energy storage power plant staffing all the expenses. The price of labor cost is driven by the number of workers of the ECS, the yearly wage price, and the price of welfare and labor insurance coverage.
Crg = Nrg-Srg -( 1+ Rf) (16)
Where N signifies the number of personnel of the electrochemical storage plant; S. represents the yearly team wage allocation; R, signifies the well-being labor insurance price.
The monetary expense connected with constructing an electrochemical power storage space plant can be substantial and is commonly funded via lasting borrowing. The price of this funding is established by the quantity of the loan and the rates of interest charged by the lending institution.
A stands for the financing amount, while R stands for the lending interest rate.
6. Tax obligations. Taxes and costs are all the tax obligations and charges to be paid for the whole life cycle of the electrochemical energy storage power plant. The details estimation is carried out in accordance with the nationwide tax obligation price laws.
Costs connected to management, such as traveling costs, workplace costs, and ecological prices, throughout the entire life-span of the electrochemical energy storage center are described as management expenses. These expenses are figured out as an established figure and are examined during the disposal stage.
The last stage in the whole life cycle of the electrochemical energy storage nuclear power plant is the disposal phase, and in the disposal phase of the electrochemical energy storage power plant, it is generally required to dispose of the relevant tools and structures, such as taking apart and reusing. Amongst them, the disposal cost refers to the cost sustained by the electrochemical energy storage power plant at the end of its valuable life because of the disposal of relevant tools and buildings and various other business activities however a particular amount of revenue will also be generated in the reusing procedure of the related devices and structures, i.e. reusing profits, which mostly refers to the carp sources, vanadium sources and other rare-earth element resources consisted of in the electrochemical power storage space power station, because of the restricted natural resource endowment in China, while the electrochemical power storage space sector is undertaking Due to the minimal endowment of natural resources in China and the fast growth of the electrochemical energy storage space industry, combined with the reality that a number of foreign countries are purely managing the export quantity of such resources, the cost of potassium sources, vanadium sources and various other rare metal sources has actually raised considerably over the last few years, and the future revenue generated from recycling of rare-earth element sources in the electrochemical energy storage power plants will certainly be very considerable. As a result, the price of disposal stage is the distinction between disposal expense and reusing revenue.
Ihs = lower jaw zone + reduced jaw symphysis + Interosseous space (19)
Where, C, represents the price of disposal; C signifies the price of disposal; I signifies reusing income; I represents the earnings from recycling buildings; I denotes the earnings from reusing rare-earth element resources; l denotes the earnings from reusing devices.
The research on taking care of the overall expense of electrochemical energy storage space power plants throughout their entire life expectancy discloses that costs can be accurately approximated by splitting the life process into four stages: design, construction, operation and maintenance, and disposal. By incorporating relevant solutions, it was identified that the substitute, power loss, and disposal expenses are essential parts of the complete life cycle expense and should be provided considerable interest. Coming close to the issue from the viewpoints of cost, sources, and environmental management is necessary to steer ventures in the direction of healthy competitors and sustainable sector growth. The layout phase plays a critical duty in affecting prices throughout all life cycle stages, stressing the value of expense management throughout this stage to control most of expenses throughout the entire life process.
The market needs to put even more emphasis on substitute cost, energy loss expense, and disposal price. Firstly, when selecting batteries, the focus should be on the overall cost of ownership over the entire life expectancy, as opposed to simply the initial investment price. This will promote healthy and balanced competition amongst organizations. Second of all, it’s necessary to take into consideration the energy loss expense, which is the price of inadequacies in converting electrical power. The price of electrical energy can considerably influence the overall expense. Finally, the expense of disposal is critical, thinking about the ecological effect and resource restraints. Presently, there are very few electrochemical power storage space plants in China, and recycling and reusing made use of batteries need even more attention. In addition, the disposal price of electrochemical power storage plants is typically ignored in investment choices, with only oil and gas extraction clearly discussed in accounting common regulations. For instance, potassium iron phosphate innovation, one of the most significant electrochemical energy storage space modern technology, faces source shortages and high rates in the future. Nonetheless, by improving the healing and reuse of rare metal resources in iron phosphate batteries, the industry can reduce costs, protect the setting, lower the explosion threat of battery piling, and lessen the dependancy on resource imports.
Today, when faced with the industry’s absence of lasting preparation in the style stage, incorrect price prediction in the operation and upkeep stage, and inappropriate consideration of the expense of the disposal phase, business must think about the whole life process expense of the electrochemical energy storage power plant when making investment choices, and look for to decrease the whole life process cost. It is recommended that enterprises should affix terrific significance to cost monitoring in the style phase when making investment decisions, and should consider the whole life cycle costs at the beginning of investment decisions, and the costing of electrochemical energy storage space plants should be thought about from the perspective of the whole life cycle.
The cost monitoring of electrochemical energy storage plants need to consider the entire life process cost throughout the style stage, implement intelligent and scalable price decrease measures during operation and upkeep, and enhance source healing rates during disposal to lessen expenses. This includes strict equipment option throughout preparation and design, focusing on technology, safety, and economic climate. Additionally, the business needs to authorize a recycling agreement with battery providers to secure future recuperation earnings, boost automation and intelligence degrees, and establish neglected storage terminals to decrease maintenance prices. The business needs to likewise comply with a scale-based approach, develop local repair work groups, and form lasting arrangements with distributors. Additionally, leading enterprises can advertise the development of rare-earth element recycling and reuse systems, in addition to battery ladder application devices. Lastly, the venture ought to constantly boost its life cycle expense administration program in day-to-day technique to boost its price advantage in the market.
The journey of energy storage space nuclear power plant, from fertilization to decommissioning, is a complicated one packed with different costs. By recognizing and preparing for these expenses throughout the entire life process, stakeholders can make sure the practicality and sustainability of these essential properties in our power landscape.
Table of Contents Selecting the right pad-mounted transformer requires careful consideration of several critical
The primary function of the pad mounted transformer is to serve as a critical distribution
A pad mounted transformer operates through electromagnetic induction, serving as a crucial distribution component that