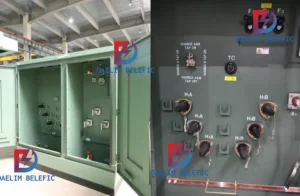
How to Choose Pad Mounted Transformer?
Table of Contents Selecting the right pad-mounted transformer requires careful consideration of several critical
ELECTRIC, WITH AN EDGE
The electrical equipment load is increasing day by day, and the transformer is a vital equipment in the electrical system, its working condition directly affects the performance of the electrical system.
750kva transformer work will generate a lot of heat, if the heat will not be eliminated in time, will directly threaten the safe operation of equipment and insulation life.
Especially in summer, when the heat dissipation conditions are already bad, many 750kva transformer equipment runs at full load for a long time, bringing a serious test to the safety and reliability of 750kva transformers. Therefore, it is of great significance to design a heat sink for 750kva transformer equipment to meet the requirements as a prerequisite to guarantee its normal operation.
As far as the form of heat dissipation is concerned, the common heat dissipation methods are mainly air-cooled and water-cooled, among which the water-cooled method is superior. Therefore, in recent years, water-cooled heat sinks are widely used.
The peak heat generation of 750 kVA high power transformer is about 12kW, in order to meet the requirements, a set of water-cooled radiators need to be designed to maintain the average surface temperature of this transformer of 750 kva 90℃.
Assuming a heat dissipation capacity of 1kW per radiator, a rectangular shape of 600mm x 300mm radiator with a water flow rate of 0.333m3/h and an inlet water temperature of 40°C is required according to the space structure of the 750 kva transformer.
According to the use requirements, in order to meet the heat dissipation and reliability, etc., the engineers designed an overall flat plate type water-cooled radiator, whose structure is shown in Figure 1.
The radiator has several independent cylindrical runners machined inside the metal plate, and the external runners are connected in series by semicircular bends. The cooling water enters the runners from the inlet and flows out from the outlet after passing through each runner in turn, during which the cooling water maintains a stable temperature of the 750kva transformer by heat exchange with the metal plate.
In this paper, the radiator structure is partially improved based on the above-mentioned radiator structure, and an overall flat plate radiator is designed as shown in Figure 2.
The radiator is made of two metal plates welded together as shown in Fig. 2. The plates are directly injection molded, and the plates are designed with “S”-shaped cooling water channels with rectangular cross-sections.
Because the flow channel inside the metal plate has been connected to itself as a whole, so there is no need to connect another external bend, at the same time, the radiator increases the volume of the cooling water channel occupancy. As a result of the above design, the radiator can effectively save materials, beautify the appearance, and simplify the processing process.
According to the basic principle of heat conduction, the thermal conductivity of the heat-conducting material is the key factor affecting the heat transfer effect. And in the process of use, the corrosion resistance of metal materials plays an important role in the life of the equipment.
Commonly used thermal conductivity materials are generally copper, aluminum, titanium and other metal materials. Among them, titanium has the best corrosion resistance, but the lowest thermal conductivity, only 15 W / (m-K); aluminum has a thermal conductivity of 237 W / (m-K), but its corrosion resistance is poor.
While the thermal conductivity of copper is 400 W / (m – K), corrosion resistance is also stronger, so comprehensive consideration of heat transfer performance and corrosion requirements, the design of copper as the heat sink thermal conductivity material.
The welding process uses silver bar welding, silver bar melting through the capillary force of the plate seam into which can achieve a good welding effect.
At the same time, the silver strip welding can ensure that the strength, anti-corrosion and leak-proof performance of the radiator will not be reduced, and the hidden danger of leakage and false welding can be eliminated through the gas-tightness and water-pressure pressure-holding test.
According to the requirements of use, this paper designed a 600mm high, 300mm wide, 15mm thick overall flat type radiator, as shown in Figure 3. The heat dissipation capacity is 1kW and the design uses fresh water as the cooling medium with a mass flow rate of 333kg per hour (0.0925kg/s).
According to the conditions of use, the radiator and transformer of 750kva double-sided contact, heat dissipation capacity of 1kW. cooling water inlet temperature of 40 ℃, the mass flow rate of 0.0925kg / s, the specific heat capacity of 4182J / (kg – ℃). Cooling water flow through the “S” shaped runner cross-sectional size: 15mm × 8mm. radiator and air contact surface for the four narrow end face, in the thermal calculation, and the air convective heat transfer can be ignored.
Cooling water inlet and outlet temperature difference is: 2.6 ℃, so the cooling water outlet temperature is 42.6 ℃. This shows that the average temperature of cooling water is: 41.3℃.
From the above, the cooling water in the flow channel and the heat transfer mode of the radiator should be forced convection heat transfer, the forced convection heat transfer coefficient of water is about: 1000 ~ 15000W / (m2 – K).
According to the radiator design parameters, the heat exchange area of cooling water and radiator can be calculated as about 0.202m2, heat transfer power of 1000W, in order to find the heat transfer temperature difference, the convective heat transfer coefficient needs to be calculated [10].
According to the design parameters of the radiator, the runner cross-section is 15mm × 8mm rectangular, you can get the equivalent diameter of the runner D is 1.04 × 10-2m. Since the average temperature of the cooling water is 41.3 ℃, the thermal conductivity of water available at 315K [10] (0.598W/m-k) for calculation.
Since the average temperature of the cooling water is 41.3°C, the average temperature of the radiator is about 42.3°C.
This paper uses FLUENT finite element simulation software to simulate and analyze the heat transfer process of this radiator. First, the 3D modeling software is used to establish a 3D model of the radiator as shown in Figure 3.
The three-dimensional model was imported into FLUENT software to establish a three-dimensional model of the cooling water, and the copper plate and cooling water of the radiator were meshed together in FLUENT software, and the mesh is shown in Figure 4: the left side of the figure shows the mesh of the copper plate of the radiator, and the right side shows the mesh of the cooling water. The minimum size of the grid edge length is 0.33mm, the maximum 10mm, and the total number of grids is about 1.5 × 105.
After the grid division, the model temperature field is solved by using the 3D solver of FLUENT software. In the solution process, this paper follows both the law of energy conservation and the k-ξ turbulence calculation model.
Since the radiator and transformer of 750kva are in contact on both sides, the heat load of the radiator (1kW) is divided by the sum of the two planes of the radiator area to obtain the heat flow density of the radiator: 2777.8W/m2.
The cooling water inlet boundary is set as a mass inflow port with a mass flow rate of 0.0925kg/s and a temperature of 40°C. The cooling water outlet is a free flow boundary.
After setting the velocity convergence condition to 10-3 and the continuity convergence condition to 10-6 under the second-order accuracy solver, the temperature field cloud of the radiator was obtained after convergence of the iterations.
The lowest temperature of the radiator copper plate body appears near the cooling water inlet, which is about 41.43°C, and the highest temperature appears at the diagonal position of the cooling water inlet, which is about 44.63°C.
Cooling water outlet temperature of 42.66 ℃, and the previous section of the theoretical calculation of 42.6 ℃, indicating that the selection of parameters and thermal calculation of this paper is basically accurate.
This paper designed the overall flat plate radiator through the optimization of the flow channel design, can effectively save materials, beautify the appearance, simplify the processing process.
Through theoretical calculations and FLUENT simulation analysis of mutual support, can prove that the heat sink design is reasonable, good heat dissipation, can meet the transformer of 750 kva use requirements.
Download Resource
Table of Contents Selecting the right pad-mounted transformer requires careful consideration of several critical
The primary function of the pad mounted transformer is to serve as a critical distribution
A pad mounted transformer operates through electromagnetic induction, serving as a crucial distribution component that