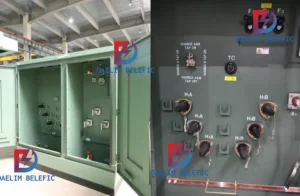
How to Choose Pad Mounted Transformer?
Table of Contents Selecting the right pad-mounted transformer requires careful consideration of several critical factors, as these ground-mounted distribution transformers play a vital role
ELECTRIC, WITH AN EDGE
1. The transformer must be well sealed during transportation and storage. During installation and operation, measures must be taken to prevent water from entering; during installation, attention must be paid to the parts higher than the oil surface of the oil pillow, such as the top of the casing, the explosion-proof membrane, the top of the oil pillow, and the airway. The sealing should be really good. , And conduct a leak test, and check the sealing condition of these parts in conjunction with maintenance every year.
2. For transformers with strong oil circulation, ensure that the connection between the body and the cooling system is well sealed during installation. Sealing gaskets should be installed correctly and kept intact. Defects in manufacturing should be handled properly, such as the rubber gasket of the submersible pump, the sealing packing of the oil inlet valve stem, and the connecting pipe of the differential pressure relay. When replacing rubber pads, samples of rubber pad materials with unknown properties should be sampled for oil resistance test.
3. The water-cooled oil cooler and submersible pump should be tested for leaks in accordance with the manufacturer’s installation and operation instructions before installation. For several oil coolers operating in parallel, it is best to install a check valve at the outlet of each submersible pump to prevent the oil flow in the spare oil cooler from reversing. The oil cooler in operation and standby must ensure that the oil pressure is greater than the water pressure.
The oil inlet valve of the submersible pump should be fully opened, and the oil outlet valve should be used to adjust the oil flow to avoid negative pressure. During operation, the indications of the differential pressure relay and the pressure gauge should be monitored regularly, as well as whether there are oil splashes in the outlet water (each oil cooler should be equipped with a drain valve to monitor whether there are oil splashes in the outlet water).
4. The explosion-proof cylinder should be connected to the oil pillow or connected to the atmosphere through the respirator. Regularly drain the water accumulated in the lower part of the oil pillow.
5. The oil seal of the respirator should be refueled and maintained to ensure smooth flow. The dryer should be kept dry.
6. Transformers of 220 kV and above should be filled with vacuum oil to eliminate air bubbles in the coil. 110 kV transformers should actively create conditions for vacuum oil injection.
7. Before the transformer is put into operation, pay special attention to removing the internal air. For example, the remaining air should be removed from the high-voltage casing flange, riser, dead zone in the oil pipeline, and the top of the oil cooler.
Before the strong oil circulating transformer is installed and put into operation, all cooling equipment should be started to circulate the oil for a longer period of time to allow the residual air to escape.
8. When charging or filtering oil from the oil pillow, the water in the oil pillow should be drained first. Oil should not be injected from the bottom of the transformer to prevent air or water and debris from the bottom of the box from being brought into the coil.
9. When the light gas sends a signal, take the gas (even air) in time to identify the composition, and take the oil sample for chromatographic inspection to find out the cause and troubleshoot in time.
Table of Contents Selecting the right pad-mounted transformer requires careful consideration of several critical factors, as these ground-mounted distribution transformers play a vital role
The primary function of the pad mounted transformer is to serve as a critical distribution transformer that steps down higher primary voltage from utility distribution
A pad mounted transformer operates through electromagnetic induction, serving as a crucial distribution component that converts high voltage electricity to lower, usable voltages for residential
When looking for the best pad-mounted transformer manufacturer, it’s important to find industry leaders known for reliability and innovative solutions. Pad-mounted transformers are essential in
After filling in the contact information, you can download the PDF.