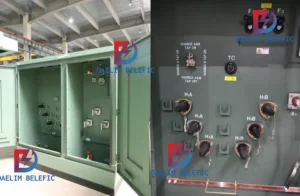
How to Choose Pad Mounted Transformer?
Table of Contents Selecting the right pad-mounted transformer requires careful consideration of several critical
ELECTRIC, WITH AN EDGE
In the world of transformer design and manufacturing, the debate over using aluminum vs copper transformer windings is a longstanding one. Both materials offer unique benefits and challenges, influencing key factors such as efficiency, cost, weight, and longevity. This comprehensive guide will delve into the most frequently asked questions about aluminum and copper transformer windings, discussing their properties, their impact on motor performance, their scrap value, their role in transformer efficiency and costs, and the significance of using copper foil for transformer winding. Ultimately, the choice between aluminum and copper windings comes down to a balance between cost, performance, and specific application requirements.
Aluminum and copper transformer windings have their unique sets of characteristics, each contributing to the transformer’s performance. Copper windings are generally denser and heavier than aluminum windings, influencing the transformer’s overall weight. Copper’s high conductivity, approximately 61% better than aluminum, allows for better electrical efficiency.
Despite aluminum’s lower conductivity, it has the advantage of being lighter and more flexible than copper, making aluminum windings easier to install and manage. Its lower density contributes to a more lightweight transformer, advantageous for transport and installation purposes.
On the cost side, aluminum is typically less expensive than copper, largely due to the differences in raw material costs. This cost-effectiveness makes aluminum windings a popular choice for manufacturers looking to keep prices competitive.
The question of which is better – aluminum or copper for transformer windings, is not a straightforward one. The answer heavily depends on the specific requirements of the transformer and its intended use.
Copper windings, with their superior conductivity, can handle higher electrical loads more efficiently, making them ideal for situations where maximum performance is needed. In addition, copper’s superior thermal properties mean that it is less prone to overheating, a key factor in the longevity of a transformer.
Aluminum windings, on the other hand, are more cost-effective and lightweight, making them ideal for situations where budget and weight constraints are significant factors. While aluminum’s conductivity and thermal properties are less than those of copper, advancements in winding technology and design have significantly narrowed this performance gap.
In summary, the choice between aluminum and copper windings depends on balancing factors such as cost, weight, performance, and longevity.
In motor applications, the choice between copper windings and aluminum windings is guided by a similar set of considerations as in transformers. Both materials have their advantages and disadvantages, depending on the specific use case.
Copper, with its superior electrical and thermal conductivity, provides better efficiency and heat resistance. This can translate to a motor that performs better under heavy load conditions and has a potentially longer lifespan due to less heat-related wear and tear. However, the downside of copper is its cost and weight, which can increase the overall cost of the motor and pose challenges for installation and transportation.
Aluminum windings are less expensive and lighter, making them a cost-effective and practical choice for motors where high performance is not the paramount concern. Despite its lower conductivity, aluminum can still offer sufficient performance for many applications, particularly with modern winding designs that optimize the use of the material. The main disadvantage of aluminum is its lower thermal resistance, which can lead to higher operating temperatures and potentially shorter motor lifespan if not properly managed.
When considering the scrap price of transformers, there is a noticeable difference between aluminum and copper. Copper, being a more valuable material, typically has a higher scrap price than aluminum. This difference can influence the end-of-life value of a transformer, potentially offsetting some of the upfront costs of a copper transformer.
However, it’s important to note that scrap prices fluctuate based on market conditions, including supply and demand and global commodity prices. Therefore, while copper generally holds a higher scrap value, the exact difference in price will vary over time and region.
The process of scrapping a transformer also involves costs, including dismantling, material separation, and transportation to a recycling facility. These costs can eat into the net scrap value and should be considered in any cost analysis of transformer materials.
Copper and aluminium, as transformer winding materials, each bring distinct properties to the table, which directly affect the performance of a transformer. Copper’s superior electrical conductivity results in less resistance, which means less energy loss in the form of heat. This translates into a more efficient transformer that can handle higher loads.
On the other hand, aluminium, while having a lower conductivity than copper, is significantly lighter and more malleable. This makes aluminium windings easier to work with during the manufacturing process and results in a lighter transformer, which can be beneficial during transportation and installation.
The thermal properties of the two materials also play a critical role. Copper’s better heat dissipation helps in maintaining the transformer’s optimal operating temperature, thus improving its lifespan and reliability. In contrast, aluminium has a lower thermal conductivity, which can lead to higher operating temperatures and may require additional cooling measures.
The weight of copper winding in a transformer can have a considerable impact on its efficiency. Copper, being a denser material, leads to a heavier transformer. However, the advantage of copper’s high electrical conductivity is that it can carry more current per unit of volume, making for more compact and efficient windings.
A heavier transformer, while posing challenges in terms of transportation and installation, often implies better performance and efficiency due to the high conductivity of copper. However, the transformer design and the winding technique also significantly influence efficiency. Therefore, while copper’s weight can hint at a transformer’s efficiency, it’s only one piece of the overall puzzle.
When it comes to the cost of transformers, the price difference between copper and aluminium can play a crucial role. Copper, being a more expensive material than aluminium, contributes to a higher upfront cost for transformers with copper windings. This is one of the main reasons why manufacturers may opt for aluminium windings, particularly for cost-sensitive applications or markets.
However, the total cost of ownership of a transformer should also consider other factors such as efficiency, maintenance costs, lifespan, and scrap value. Copper windings, due to their higher efficiency and longer lifespan, may result in lower operational costs over time, partially offsetting the higher initial cost. Additionally, the higher scrap value of copper can contribute to a higher end-of-life value for copper transformers.
There are several reasons why one might choose a copper-wound transformer over an aluminium-wound one. The primary advantage of copper windings is their superior electrical conductivity, which results in a more efficient transformer that can handle higher loads. Copper’s better thermal properties mean it’s less likely to overheat, contributing to improved reliability and lifespan.
However, it’s important to consider the application-specific needs. For high-performance applications, where efficiency and reliability are paramount, the benefits of copper windings often justify the higher cost. For less demanding applications or where budget constraints are significant, the cost-effectiveness of aluminium windings may be more appealing.
Additionally, factors like weight and installation ease may influence the decision. Copper transformers, due to their heavier windings, can be more challenging to transport and install than their aluminium counterparts.
Copper foil is often used in transformer windings due to its excellent electrical conductivity and flexibility. Its thin, flat nature allows for tight, efficient winding configurations that can improve transformer performance by reducing electrical losses.
One of the key advantages of copper foil for transformer winding is its ability to carry high-frequency currents effectively, making it suitable for applications like switch-mode power supplies and certain types of audio transformers.
However, copper foil is more expensive than wire and is typically used in specialized applications where its benefits outweigh the cost. It also requires specific handling and winding techniques, further contributing to the cost.
The longevity of a transformer is largely determined by the quality of its construction, maintenance, and operating conditions. However, the choice of winding material can also play a significant role.
Copper windings, due to their superior electrical and thermal conductivity, are generally less prone to overheating than aluminium windings. Overheating is one of the primary causes of transformer failure, as it can lead to insulation breakdown and other forms of damage. Therefore, copper windings can contribute to a longer transformer lifespan.
Aluminium windings, while less conductive, can still provide reliable service, particularly with modern winding techniques and designs that optimize the material’s performance. However, aluminium windings may require additional measures, such as cooling systems, to manage operating temperatures and ensure a long service life.
In conclusion, both copper and aluminium windings can offer good longevity, with the edge typically going to copper due to its superior electrical and thermal properties. However, many other factors, including transformer design, quality of construction, and maintenance, will also heavily influence a transformer’s lifespan.
Download Resource
Table of Contents Selecting the right pad-mounted transformer requires careful consideration of several critical
The primary function of the pad mounted transformer is to serve as a critical distribution
A pad mounted transformer operates through electromagnetic induction, serving as a crucial distribution component that
After filling in the contact information, you can download the PDF.